In October 2024 an Airbus-led EU-funded consortium unveiled the Multifunctional Fuselage Demonstrator, mostly made of carbon-fibre-reinforced thermoplastic polymer composites that cost-effectively reduce an aircraft’s structural weight by over 10% and make components easier to reuse and recycle than traditional metal or carbon-fibre parts. As new aircraft take flight – Cirium Ascend Consultancy estimates around 45,900 new passenger, freighter and turboprop aircraft will be delivered globally between 2024 and 2043 – such tie-ups can enhance value recovery when these vehicles are retired. This is also true for repurposing aircraft and harvesting spare parts.

Aerospace firms strive to curb waste when retiring aircraft
UK-based Cirium Ascend Consultancy estimates 84% of in-service passenger aircraft and 73% of in-service freighters will be retired by 2043
Value chain: downstream
Aerospace
AT A GLANCE
As new aircraft jet into the world’s fleet, plane retirements are accelerating too.
On average, up to 90% of a retired aircraft's bulk is recycled or reused; firms seek to boost this share amid growing investor, financier, regulator and public scrutiny.
To do so, many are improving materials usage and recovery, repurposing aircraft, harvesting spare parts and collaborating.
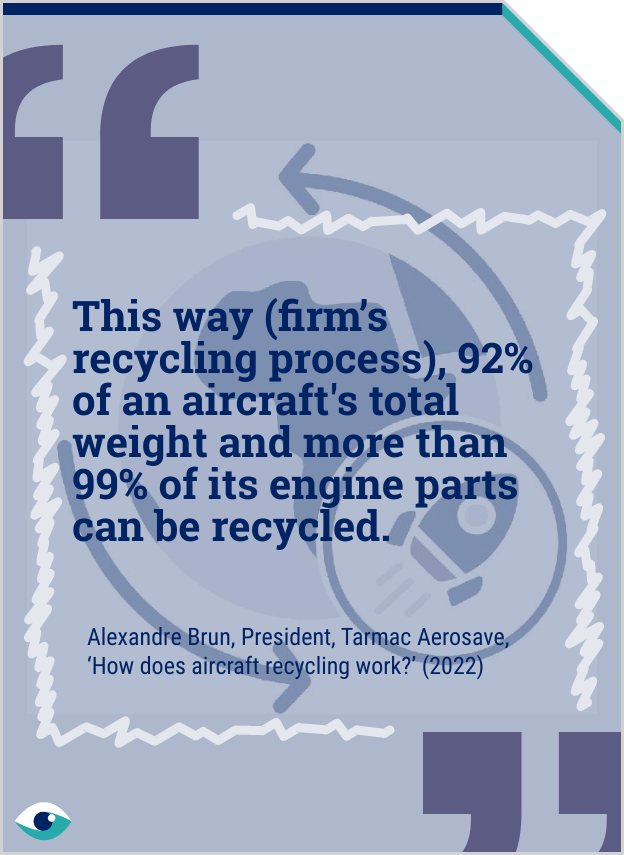
Repurposing aircraft
Converting retired passenger aircraft into freighters, which tend to be retired later, prolongs their utility. Under its A330P2F and A320/321P2F programmes, Airbus, in collaboration with ST Aerospace and Elbe Flugzeugwerke, their joint venture, has converted hundreds of its A330 wide-body and A320 and A321 narrow-body aircraft that have completed useful operational service as commercial jetliners into freighters. Old planes can be repurposed as art, furniture and educational displays as well.
Harvesting parts
The International Civil Aviation Organisation estimates 40–50% of a dismantled aircraft’s bulk is returned to the parts distribution pipeline. Certified refurbishing engines, avionics, landing gear and other high-value parts of decommissioned aircraft can be reused and resold, providing significant value recovery while supplying buyers with cost-effective parts for other aircraft. Safran and GE Aerospace participate in the recovery of such used parts through their subsidiary, CFM Materials.
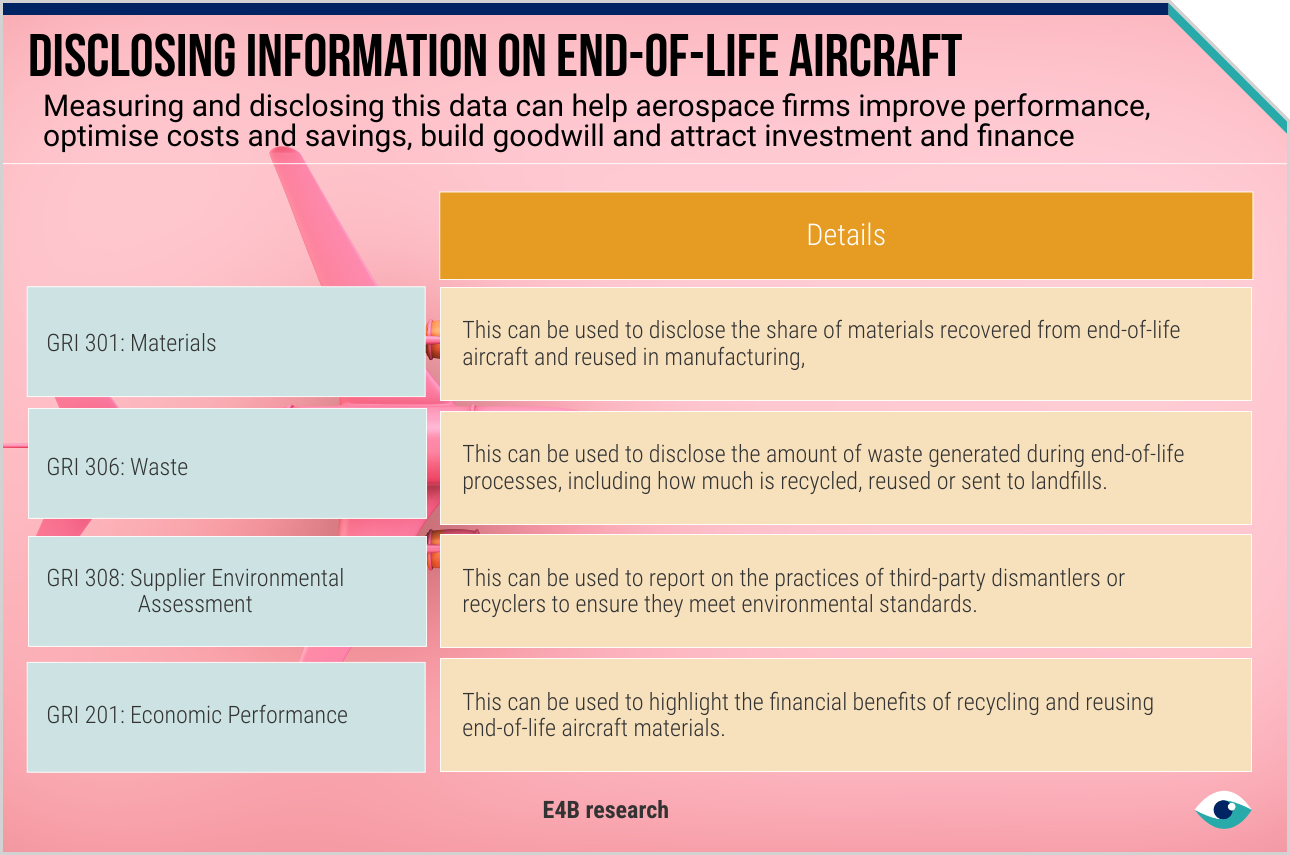
Material use and recovery
Most unsalvageable parts of disassembled aircraft are scrapped, recycled and returned to the supply chain as raw materials – notably, aluminium, titanium and steel – curbing demand for virgin materials. Durable and lightweight carbon and glass fibre composites are common in newer aircraft, but hard to recycle and can end up being discarded and sent to landfill. In April 2024 Boeing opened a research and technology centre in Japan to find new ways to recycle composite material.
Collaboration
Tie-ups can propel efficiency. Tarmac Aerosave, in which France’s Airbus, Safran and Suez hold stakes, has dismantled and recycled at least 339 aircraft and 186 engines, with a recovery rate of over 92% of the aircraft’s weight. The Aircraft Fleet Recycling Association, whose members include Boeing and Brazil’s Embraer, sets best practices for sustainable aircraft disassembly and salvaging and recycling aircraft parts and materials; and offers accreditation to firms that observe the guidelines.